ECO
XLANCE® makes elasticity sustainable
Clean process, durable and recyclable fabric
We make it clean
We make it clean
We make it clean
We make it clean
We make it clean
We make it clean
We make it clean
We make it clean
We make it clean
We make it clean
We make it clean
We make it clean
We make it clean
We make it clean
We make it clean
We make it clean
We make it clean
We make it clean
We make it clean
We make it clean
We make it clean
Solvent Free
XLANCE® is produced through a clean melt spinning process, different from the dry-spinning (chemical) one of spandex that involves the use of dangerous solvents like DMAC or DMF.
Renewable energy
XLANCE® is sourcing 100% of its electric power needs from renewable energy.
Low CO2 Emissions
XLANCE® can be heat set at just 120°C ensuring the manufacturers substantial energy and costs savings and a relevant reduction in CO2 emissions.
The test was performed on rameause with 10 vertical chain fields fed with natural gas indirect (CH4).The reduction in temperature to carry out the fabric thermofixing operation allows to reduce the consumption of natural gas (CH4) by 32 mc/h and consequently to reduce CO2 emissions by 44% (reduction of CO2 emissions by 63.1 Kg/h of CO2).
We make it durable
We make it durable
Extended life cycle
XLANCE® features a long-lasting stretch which guarantees an extended life cycle to all garments made of it. This entails a lower resource consumption and waste production, for a lower environmental footprint.
Low microplastic release
Thanks to its extreme chemical/ physical resistance, XLANCE® has no tendency to fragmentation and microfiber shedding, not even after exposure to harsh agents, weathering or ageing.
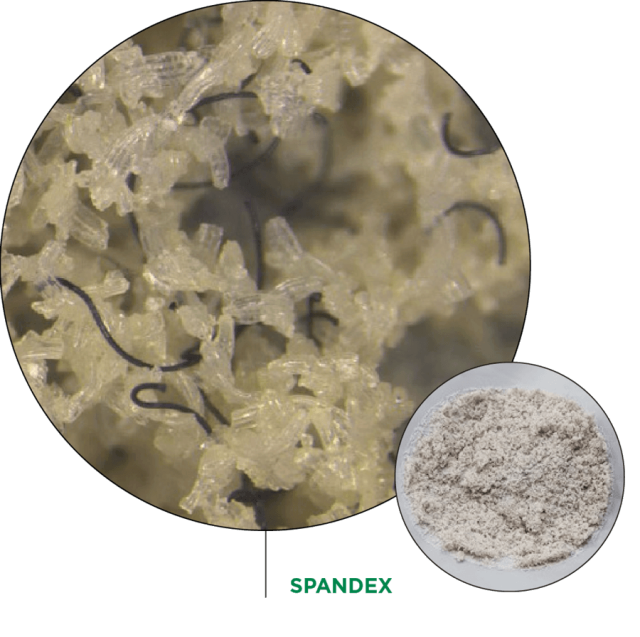
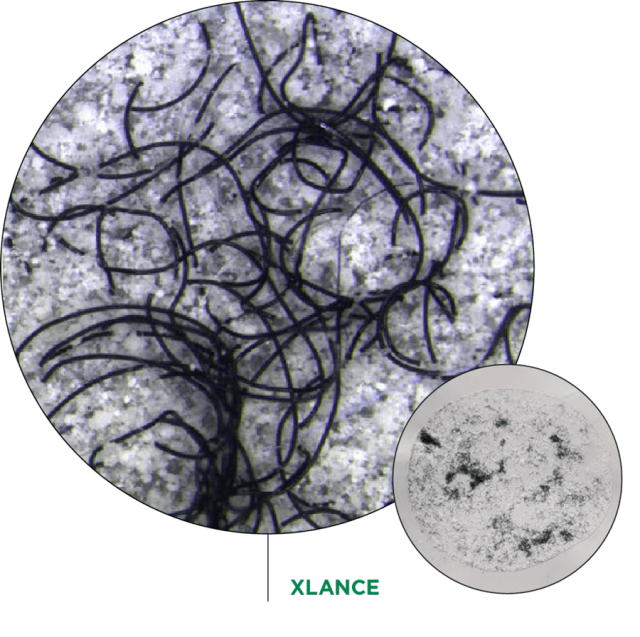
PA6-based warp-knitted fabrics containing either 20% XLANCE® or 20% spandex were exposed to
a combination of sunscreens and sunlight (Xenotest – ISO 105-B02, for 200 hours), to simulate a typical beachwear/outdoor cloth usage; washing was performed at 40 °C according to ISO 105-C06, procedure A1S (with 25 steel balls and ECE detergent). Collection of microfibers was performed by filtering wastewaters from the washing machine on 25-micron-mesh filters; microfibers (dimensions <
5 mm) were quantified and identified by gravimetric analysis and microscopic observation. XLANCE® microfiber release is negligible, whereas spandex yarn releases an average of 20 g of microfibers per kg of fabric.
We make it circular
Make it circular
XLANCE® is always looking for new solutions that make sustainable not only the product, but also the entire production process, having a more systemic and holistic vision of the entire textile chain. The chemical component separation and material regeneration is one of the solutions that XLANCE® is trying to put in place, in the perspective of a sustainable development.